Multihead weighing approach
The continuing development and enhancements of multihead weighing technology has made a huge contribution to mixed products. Today there are weighers with 16, 18, 20, 24, 28, and even 32 heads, mixing up to eight different products simultaneously for discharge into the same pack. Machines can even be linked together to handle a virtually limitless number of mixed products within one line. There are numerous benefits of the mixed weighing approach. One machine can effectively do the work of two or more, saving on operator and maintenance costs as well as significantly reducing space requirements in the factory. Each section of the weigher is dedicated to a different product type and these can be set precisely at different target weights, ensuring that the right mix of items is consistently included in each pack and that the more expensive items in particular, for example higher value cashew nuts in a fruit and nut mix, are tightly controlled. The multihead mixed weighing approach typically offers increases in speed, accuracy and efficiency compared to pre-mixing. Keeping products separate until they are packed can also help to minimize damage compared to more mechanical pre-mixing processes. Mixed weighing technology also continues to evolve, and the faster processing technology and very precise product transfer now available mean new levels of competitive advantage can be achieved. While products can be weighed and discharged simultaneously, an alternative technique called consecutive topping allows the proportion of the cheaper ingredients in the total weight to be varied, to both improve accuracy and save money. Consecutive topping works by making the target weight for each product take account of the actual weight of the previous component in the mix instantly and without delay. This compensation approach greatly helps improve overall accuracy by preventing allowable errors from adding together. Some customers also require guaranteed low piece counts in mixes down to single pieces. For this, precise designs and software are available to feed very controlled piece counts and, if necessary, reject over weights mid-cycle to ensure that exceptional accuracy and efficiency is maintained at the machine outlet.

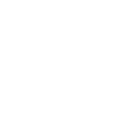
Accuracy and efficiency
High head machines can be configured to feed multiple lines. And as well as its ability to handle different mixes, the same weigher can be configured to handle a single product for discharge simultaneously in up to eight different packs - delivering extremely fast speeds of up to 440 packs every minute. It is also possible to combine smaller mixes and discharge these into multiple outlets. When choosing a mix or multiple outlet weighing solution, there are a number of factors to consider. Clearly accuracy and efficiency are essential but these need to be taken into account alongside the required speed of the line. It is very important that sufficient weigh heads are allowed per item in the mix to ensure a stable combination can be achieved for weigh calculations each time. At the same time, the overall speed of the weigher will be dependent on the section using the fewest number of heads - so the more heads available (combined with enhanced weighing technology), the faster the potential speed. Of course, the nature of the product needs to be carefully considered. This will influence the angles, shapes and materials used in contact parts design, which will be critical to ensure effective product transfer through the weigher. Similarly, a compatible interface with the bag maker or distribution system is necessary to ensure that fast and efficient throughput is maintained. Size of the hoppers will also be dependent on the pieces size, bulk density and target weight of products being handled. It is worth therefore taking the time to assess your requirements in detail - including both current needs and potential future requirements - and then discussing these with your professional multihead weigher supplier to ensure that you have a solution that delivers the right mix of product and profit.

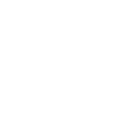
Email: ian.atkinson@ishidaeurope.com
Web: www.ishidaeurope.com