Expanding information analytics
Information analytics is a broad category of software-driven intelligence that enables a smart sorter to collect, analyze and share useful information across the processor's enterprise. This highly customized capability can collect real-time data and batch reports about the sorting process and every product and object flowing through the sorter, whether that data is used to make sorting decisions or not. By turning data into knowledge, it improves the sorter's accept/reject decisions and enables more informed decisions about the processes upstream and downstream of the sorter. What's new is the ease with which this powerful capability can be harnessed. Today's most sophisticated digital sorters feature advanced software that enables universal connectivity. These sorters can easily integrate with virtually any factory automation system such as MES or SCADA from any manufacturer, using any software protocol. In addition, they can be equipped with a PLC personality that facilitates integration with PLC networks via web browsers, Ethernet/IP and Modbus devices. Of course, these sorters also enable data to be collected in a database format for offline analysis. Other new aspects of Information Analytics come from recent refinements that ease the selection of specific data categories that are of interests to each processor, as well as software that enables custom-designed 'dashboards' on the sorter's user interface. For example, a processor might wish to see 'at a glance' information such as the current trend in incoming product attributes or trends about the occurrence of various defects over time. This data could be illustrated as a table or a line graph or a bar chart that refreshes at specific intervals. The dashboard can be viewed on the sorter's touchscreen as well as remotely on a computer off the plant floor or on a smart phone or other mobile device. These remote connectivity capabilities support the notion that modern digital sorters can self-adjust and maintain optimal performance autonomously, without the need for human supervision during normal operations.
Easing use

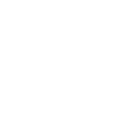
Digital sorters are getting more capable and sophisticated at the same time the labor pool is shrinking, making it harder to attract and retain good equipment operators. These dueling trends make it imperative that the sorter's user interface (UI) be simple and intuitive and that automation features reduce reliance on line operators. A goal of software engineers working to improve the UI is to allow 100 percent of the sorter's potential to be realized by operators with no technical specialization after only a few hours of training. What's new with the latest user interfaces is an evolution in design that leverages people's familiarity with smart phones and mobile apps. By mimicking the actions and gestures, such as swiping and tapping, and the visual organization of information that people have grown accustomed to on their phones, the sorter becomes dramatically more intuitive to operate. Ergonomic design, less screen clutter, better legibility and fewer steps to get from one function to another also help the process. New automation features take ease of use to another level. In addition to STG and SLC, modern sorters offer advanced auto-learning, self-adjusting capabilities, predictive system diagnostics and smart alarms that enable a sorter to operate virtually unattended during normal production.
Identifying foreign material
One of the more interesting detection developments recently introduced on the most advanced digital sorters is multi-sensor pixel fusion. Real-time pixel fusion merges data streams from multiple sensors into algorithms to make more informed accept/reject decisions. Fusing data at the pixel level increases the contrast between 'good' and 'bad' (as defined by the user) to enable the sorter to detect and remove more subtle defects and difficult-to-detect FM such as glass. In addition to improving product quality while increasing yields by removing more FM and defects and reducing false rejects, pixel fusion allows the sorter to actually identify the specific types of FM that are seen. Fusing data from multiple cameras and laser sensors creates a unique 'fingerprint' of the object, which the sorter then compares to fingerprints saved in its memory to uniquely identify the object type. Rather than simply alerting the operator that FM has been found, the sorter can tell the operator and generate reports about specific instances when glass, plastic, rubber or other specific FM types have been found. It's so accurate, it can distinguish between different types of plastics whether of the same color or not. Processors armed with this degree of data can more quickly discover the root cause of FM introduction into the product stream in an effort to prevent additional incidences. They're able to easily record detailed information about FM events, to see trends and connect incidences to other line events that may have occurred at the same time or in relation to a specific batch or supplier of product.

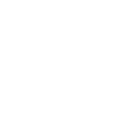
Conclusion
Intelligent sorting is evolving at a rapid rate thanks to more powerful computers and more advanced software that offer new capabilities. The driving force, of course, is delivering added value to food processors based on the issues and opportunities that are important to them. Better detection and removal of FM and product defects, greater automation, ease of use and access to data that is transformed into knowledge all help to optimize product quality, maximize yields and reduce operator intervention. By leveraging new technological advancements, early adopters can create a competitive edge.
Web: www.key.net